Unlocking the Potential of Injection Molds in China
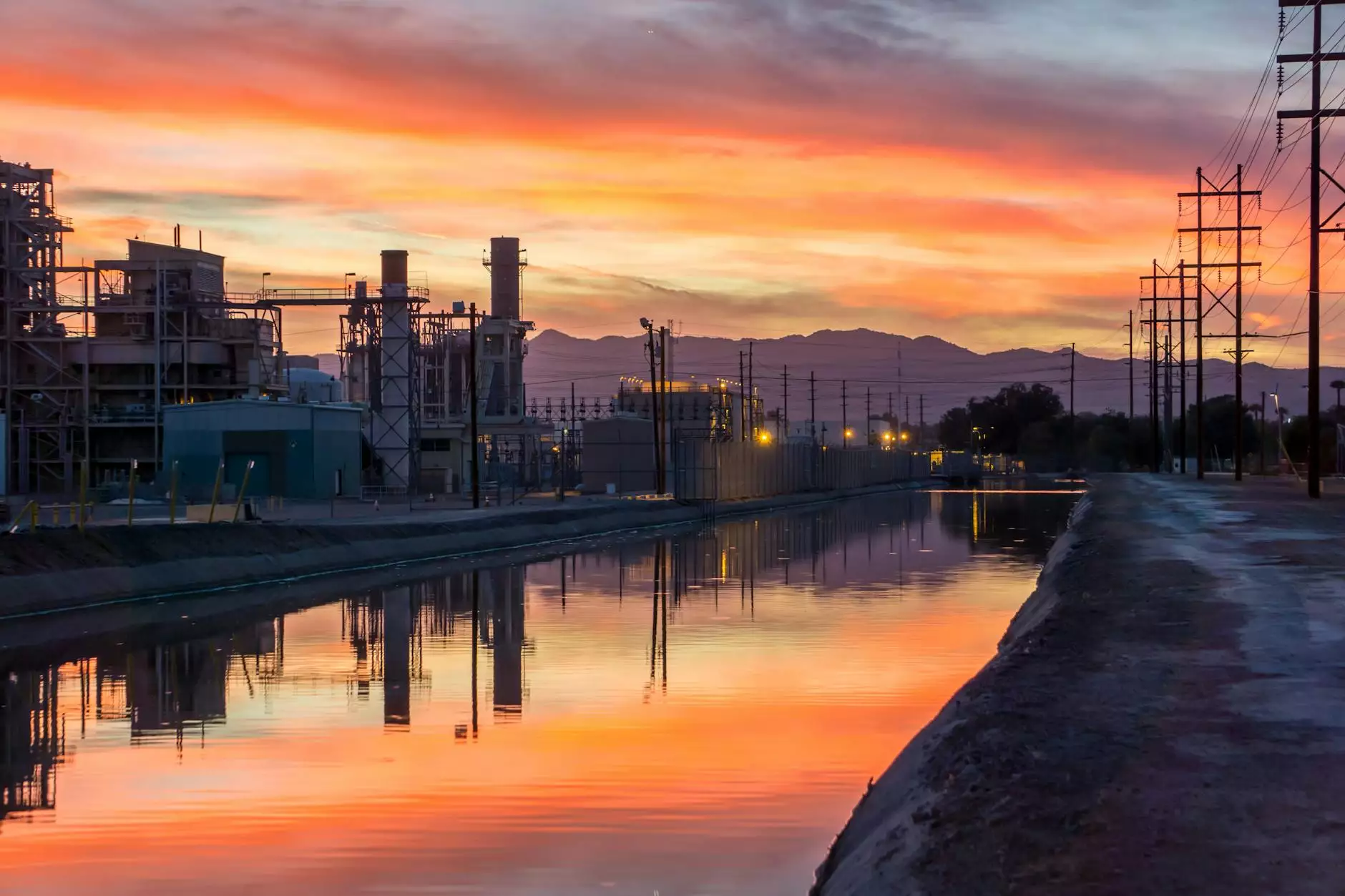
China has solidified its position as a global leader in manufacturing, particularly in the realm of injection molds. The evolution of this industry has enabled businesses worldwide to capitalize on cost-effective solutions without sacrificing quality. This article delves into the various aspects of injection molds China, showcasing how they can enhance your production capabilities.
Understanding Injection Molds
Injection molding is a manufacturing process where material is melted and injected into a mold to produce parts. This technique is widely used in various industries such as automotive, electronics, and consumer goods. The advantages of injection molds include:
- High Precision: Injection molds provide exceptionally uniform and accurate products.
- Mass Production: Suitable for producing large volumes of the same item rapidly.
- Complex Shapes: Ability to create intricate designs that may be too complicated for other manufacturing methods.
- Material Variety: Supports a wide range of thermoplastics and thermosetting materials.
The Role of China in Global Manufacturing
China's prowess in manufacturing injection molds is attributed to various factors including technological advancements, abundant labor resources, and a focus on innovation. By integrating traditional craftsmanship with high-tech solutions, manufacturers in China continue to set industry standards.
Key Advantages of Sourcing Injection Molds from China
Businesses seeking to leverage injection molds from China can enjoy significant benefits:
- Cost Efficiency: The competitive pricing of labor and materials in China results in overall lower production costs.
- Access to Advanced Technology: Manufacturers invest heavily in the latest technologies, ensuring high-quality output.
- Scalability: Transit from prototypes to mass production is seamless with Chinese manufacturers.
- Expert Workforce: Skilled technicians with expertise in advanced manufacturing techniques.
The Manufacturing Process of Injection Molds
1. Design and Prototyping
The journey of creating a product using injection molds starts with meticulous design. Engineers use CAD software to create detailed 3D models, followed by the prototyping stage. Prototypes allow manufacturers to test functionality before moving to mass production.
2. Mold Creation
Once the design is approved, the next step is mold fabrication. This process typically involves:
- Material Selection: Common materials for molds include steel and aluminum, chosen for their durability.
- CNC Machining: Precision machining ensures that molds meet intricate specifications.
- Finishing: Molds receive surface treatments to enhance performance and product finish.
3. Injection Molding
After the molds are ready, the actual injection molding process begins. Raw plastic or other materials are heated and injected into the mold under high pressure. This step is crucial for achieving the desired shape and consistency.
4. Quality Control
Quality assurance is a pivotal aspect of the manufacturing process. Each item is inspected to ensure it meets design specifications and industry standards. Through rigorous testing, manufacturers can guarantee the end product's reliability and performance.
Impact of Technology on Injection Molding in China
The integration of cutting-edge technology has transformed the injection molding landscape in China. Significant advancements include:
- Automation: Automation has enhanced production efficiency, reducing human error and speeding up processes.
- 3D Printing: Employed in the prototyping phase to reduce lead times and costs.
- Smart Manufacturing: IoT devices are increasingly used for real-time monitoring of the production process.
Environmental Considerations
As global attention shifts towards sustainability, China's manufacturing sector is adapting. Companies are implementing eco-friendly practices such as:
- Recycling Materials: Using recycled plastics in the production process.
- Energy Efficiency: Investing in machinery that consumes less energy.
- Waste Reduction: Minimizing scrap and improving resource management.
Choosing the Right Manufacturer for Injection Molds in China
Selecting a reliable manufacturer is crucial for the success of your project. Here are key factors to consider:
- Experience: Look for manufacturers with proven expertise in injection molding.
- Portfolio: Assess previous projects to gauge quality and capabilities.
- Certifications: Ensure the manufacturer complies with international standards.
- Communication: Strong communication leads to better collaboration and understanding of your needs.
Success Stories: Companies Thriving with Injection Molds from China
Many companies have successfully optimized their production lines through injection molds from China. Let's explore a few success stories:
1. Automotive Industry Innovations
One leading automotive manufacturer partnered with a Chinese company to develop lightweight components, utilizing injection molds that significantly reduced production time and costs while enhancing performance.
2. High-Volume Consumer Goods
A global consumer goods brand scaled its operations dramatically by sourcing injection molds from China. The combination of affordable costs and high production rates allowed them to meet market demands efficiently.
Future Trends in Injection Molding
The future of injection molds in China appears promising, with several trends on the horizon:
- Hybrid Manufacturing: Combining traditional methods with new technologies for better efficiency.
- Customization: Increased demand for bespoke molds as businesses seek unique designs.
- Sustainability Initiatives: Growth in eco-friendly materials and processes.
Conclusion
In conclusion, the field of injection molds in China presents vast opportunities for businesses aiming to enhance their production capabilities. The combination of advanced technology, skilled labor, and an efficient manufacturing process positions China as a key player in the global market. For companies like Deep Mould, leveraging these advantages can lead to substantial growth and innovation. Embrace the future of manufacturing by exploring the potential of injection molds in China today.